From now on, I will explain the assembly process. I excuse your understanding as the update has been delayed due to a lot of my project consulting recently.
First of all, we would like to discuss the structure of the assembled battery type that we know well. It is largely divided into three types (pouch type, cylindrical type, prismatic type), and the three also have a more subdivided structure depending on the manufacturer and purpose of use. However, for convenience of explanation, detailed differences will be omitted.
This explanation is the Pouch type.
The pouch type is easy to change in structure and shape, and it may be understood as the most optimized structure in the initial EV market due to easy capacity expansion in a structure in which several electrodes are overlapped. Moreover, along with the increase in I-Phone and Android phones, there are various types of process changes, and there are slight differences in construction methods for each manufacturer. And newly re-examined Solid state battey (actually, this technology has been reviewed since the 1990s, and it was lost due to doubts about mass production), and most of the batteries are also considering pouch types due to structural difficulties in electrodes. Although pouch type has many advantages, it is still understood as an exclusive construction method of some Asian companies. The reason why it is not applied to other companies is that it is difficult to mass-produce the construction method of the pouch type, and there is a disadvantage that the structure becomes complicated incidentally due to the structural characteristics of the pouch when made into a pack for automobiles.
The procedure of the Pouch type is largely as follows. The classical process is 1)notching 2)laminating 3)folding 4)cell assembling, and the most commonly used process is 1)notching 2)stacking 3)cell assembling. The difference is just how to stack each electrode and separator, which is more efficient in quality and productivity and cannot be easily determined. In addition, companies that manufacture facilities are also classified, and there is room for dispute to be discussed here, so it will be omitted. In Notching and cell assembly, the fundamental method is the same.
In Notching, the management of accuracy and cutting quality of the electrode is the most important in directly cutting the shape of the electrode. In addition, the speed of processing a large amount of electrodes determines productivity and competitiveness. In the construction method, technology was developed by cutting using a mechanical mold and cutting using a laser. However, what is still preferred in terms of quality is the cutting method using mechanical molds.
Next time, I will continue to explain the technology of pouch type.
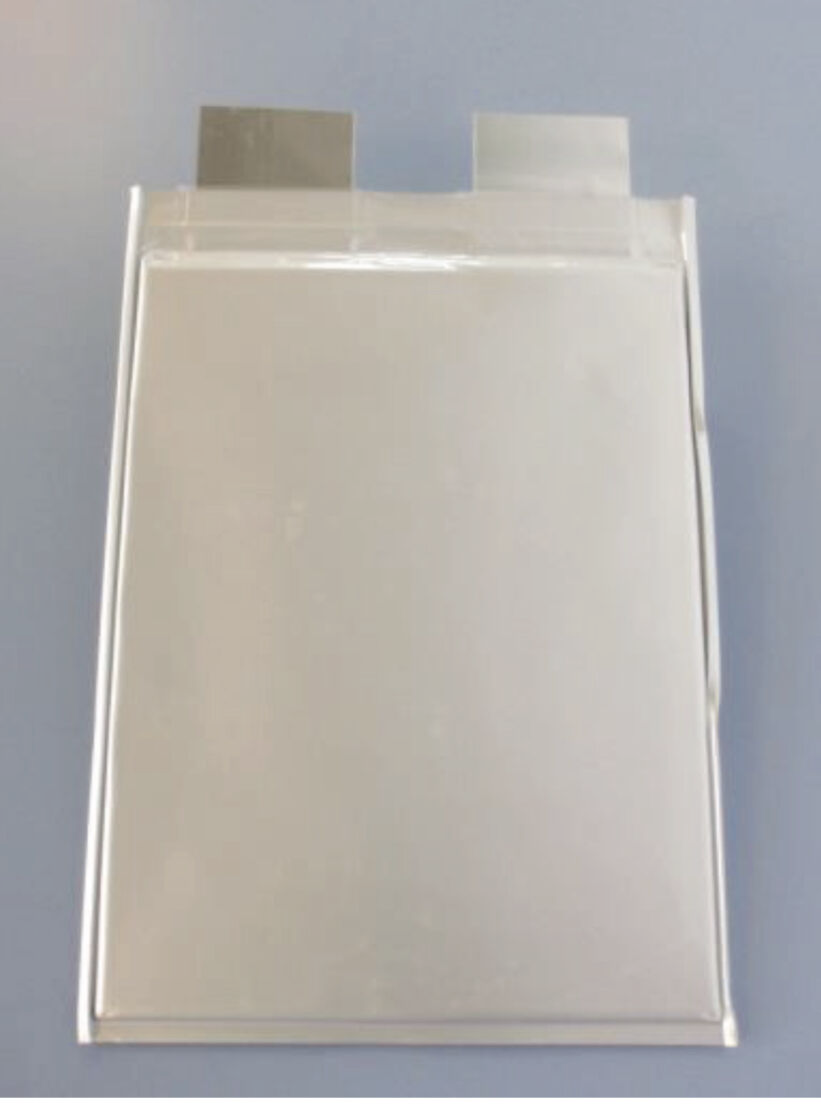
コメント